Ventilspiel prüfen – Wie wird es gemacht?
Ventilspiel prüfen ist wie Reifenluftdruck kontrollieren, nur seltener!
Den Luftdruck prüfst du selber. Aber das Ventilspielspiel?
Naja, es ist schon auch deutlich aufwändiger. Da stellt sich schon die Frage, ob du das lieber einer Fachwerkstatt überlassen willst.
In diesem Artikel erkläre ich dir, wie die Ventilspielkontrolle bei meiner Yamaha TRX 850 abläuft.
Die Vorgehensweise ist bei vielen, auch moderneren Motorrädern ähnlich.
Du liest, wie die Arbeitsschritte ablaufen und bekommst Tips und Hinweise.
Nach dem Lesen des Artikels weißt du, wieviel Arbeit es ist und worauf du achten mußt, falls du dich entschließt es selber zu machen.
Im Artikel: Was du schon immer über das Ventilspiel wissen wolltest kannst du den Aufbau von Ventiltrieben und die Theorie rund um das Ventilspiel nachlesen. Schau da bitte mal rein, es wird dir helfen die Arbeitsschritte besser einzuordnen.
Wann muß das Ventilspiel geprüft werden?
Du kannst das Serviceintervall für die Ventilspielkontrolle in der Bedienungsanleitung oder im Wartungsheft des Motorrades nachlesen.
Für die TRX 850 gibt Yamaha ein Wartungsintervall von 42.000 km oder 42 Monaten vor.
Das zeitliche Intervall ist technisch nicht begründet, es ist wohl eher ein Tribut an die lange Laufstrecke, mit der sich Yamaha vielleicht selber nicht so richtig wohl gefühlt hat.
Ich empfehle am Anfang häufiger als vorgegeben zu kontrollieren. Wenn sich nach einigen Kontrollen die Werte nicht mehr ändern, kann das Intervall verlängert werden. Länger als das vorgegebene Wartungsintervall solltest du aber auch dann nicht warten.
Ich bin mit meiner TRX wenig gefahren. Ich habe nach fast 25 Jahren nur etwas über 20.000 km auf dem Tacho. Es ist jetzt an der Zeit mal nach dem Rechten zu schauen.
Das Ergebnis der Kontrolle hat gezeigt, dass das Ventilspiel korrigiert werden musste. Also sind 20.000 km für die erste Kontrolle kein schlechter Wert.
Ventile freilegen
Als erstes müssen natürlich die Ventile freigelegt werden.
Würden wir über ein Auto reden, dann wäre es jetzt ganz einfach. Motorhaube auf, Ventildeckel runter und los gehts!
Beim Motorrad ist die Sache in der Regel etwas komplizierter. Der Zylinderkopf des Motors ist schlecht zugänglich.
Bei der TRX müssen die Verkleidung, der Tank, die Airbox und der Kühlmittelkühler abgebaut werden, damit ich an den Ventildeckel rankomme.

Die Verkleidung ist schnell abgebaut. Die Spiegel müssen ab, die beiden Schrauben rechts und links am Verkleidungshalter und die vier Befestigungsschrauben vorn am Scheinwerfer. Dann noch die Blinker abstecken, sie haben in den Kabeln extra eine Trennstelle. Das geht ohne Probleme.

Ein Benzinhahn, den man nicht zu machen kann?
Um den Tank abzubauen, muss die Sitzbank runter. Danach die lange Schraube am Tank hinten und die beiden kurzen Schrauben vorn am Tank rechts und links lösen.
Die ganz effizienten Kollegen demontieren nur die vorderen Schrauben und drehen den Tank um die lange Schraube nach hinten.
Ich baue den Tank lieber ganz aus, damit ich mehr Bewegungsfreiheit habe, also muss der Benzinschlauch ab.
Der Benzinhahn hat keine „Zu“ oder „Off“ Stellung.
Wie verhindere ich, dass Benzin ausläuft, wenn ich den Benzinschlauch abziehe?
Ganz einfach. Den Hebel auf „ON“ stellen!
Die TRX besitzt einen Unterdruckbenzinhahn.
Wenn der Motor läuft, dann öffnet Unterdruck aus dem Ansaugkanal die Benzinzufuhr zum Vergaser automatisch. Deshalb muss und kann der Benzinhahn nicht manuelle geschlossen werden.
Ist der Motor aus, dann ist kein Unterdruck da und der Benzinhahn ist abgesperrt. Deshalb kann beim Ausbau der Benzinhahn auf „ON“ stehen. Auch „RES“ funktioniert, ohne das Benzin ausläuft.
Der Hebel darf nur nicht auf „PRI“ zeigen. In dieser Stellung ist der Benzinhahn auch ohne Unterdruck geöffnet und das Benzin würde auslaufen.

Kühler ausbauen
Bevor ich den Kühler ausbauen kann, muss erst das Kühlwasser abgelassen werden.
Achtung! Niemals das Kühlsystem öffnen, wenn der Motor noch heiß ist. Das Kühlsystem steht dann unter Druck. Das heiße Kühlwasser würde heraus spritzen und kann zu bösen Verbrennungen führen.
Bei dieser Gelegenheit werde ich natürlich gleich auch das Kühlwasser wechseln. Dafür lasse ich es restlos ab. Es gibt eine Ablassschraube an der rechten Motorseite auf dem Deckel der Wasserpumpe. Eine weitere Ablassschraube befindet sich unten vorn am linken Zylinder unter dem Auspuffkrümmer.
Jetzt kann ich die Kühlerschläuche ausbauen.
Achtung an den Stutzen des Wasserkühlers!
Die Anschlussstutzen am Kühlmittelkühler bestehen aus relativ weichem Aluminiumrohr.
Ich darf an dieser Stelle den Schlauch nicht mit einem Schraubenzieher herunterhebeln! Es besteht die Gefahr, dass ich die Stutzen verbiege. Also am Besten die Schläuche auf der Kühlerseite dran lassen.
Ich entschließe mich, sie vorsichtig mit der Hand abzuziehen. Ich will gründlich prüfen, ob sie porös geworden sind.
Am Kühler ist der Elektrolüfter befestigt, dessen Anschlusskabel hinter dem Ventildeckel, unter der Airbox, am Thermostat angesteckt ist. Da die Airbox einfach von den Vergasern abgenommen werden kann, komme ich gut ran um das Kabel abzustecken.
Der Kühler kann nun abgeschraubt werden.
Bei der TRX sitzt der Kühlwasserstutzen, durch den das heiße Kühlwasser aus dem Motor heraus strömt, mitten im Ventildeckel. Er muss abgebaut werden, um den Ventildeckel abnehmen zu können.
Ich habe auch die Vergaser ausgebaut. Sie sind undicht und ich muss sie auseinander bauen und in Ordnung bringen. Damit habe ich noch etwas mehr Platz zum arbeiten.
Die Vergaser ab- und vor allem wieder anzubauen, ist am eingebauten Motor der TRX eine fürchterliche Fummelei. Nur zum Ventilspiel prüfen würde ich die Vergaser nicht ausbauen, sondern am Motor montiert lassen.
Ventildeckel abschrauben
Jetzt kann ich die Ventildeckelschrauben lösen und den Deckel abnehmen.
Der Zylinderkopf sieht dann so aus:

Die Nockenwelle, die auf der Auspuffseite liegt, ist die Auslassnockenwelle. Sie hat zwei Ventile pro Zylinder.
Die obere Nockenwelle, die sich auf der Vergaserseite befindet, ist die Einlassnockenwelle mit drei Ventilen pro Zylinder.
Ab jetzt ist Vorsicht geboten. Ich muss aufpassen, dass mir nichts in den Motor fällt!
Nockenwelle in die richtige Position für die Ventilspielmessung bringen.
Als Nächstes muss ich jetzt die Kurbelwelle in die Position drehen, in der alle Ventile des Zylinders geschlossen sind, so dass ich das Ventilspiel kontrollieren kann.
Zündkerzen lösen
Ich löse die Zündkerzen, lasse sie aber in den Kerzenlöchern stecken.
Somit haben die Zylinder beim Durchdrehen der Kurbelwelle keine Kompression und ich kann den Kolben leichter auf den oberen Totpunkt stellen. Es kann aber auch nichts durch das Kerzenloch in den Zylinder fallen.
Bei der TRX ist der Schacht für die Zündkerzen so eng, dass nur der Kerzenschlüssel aus dem Bordwerkzeug passt, weil er sehr dünnwandig ist. Ich habe Kerzenschlüssel aus meinem Werkzeugkasten versucht, keine Chance.
Nach 20.000 km leiste ich mir neue Zündkerzen, obwohl die alten eigentlich noch gut aussehen.

Kolben auf Totpunkt stellen.
Der erste Zylinder ist der in Fahrtrichtung links liegende Zylinder. Bei ihm fange ich mit der Ventilspielkontrolle an.
Dafür muss ich die Kurbelwelle in eine Position drehen, in welcher der Kolben sich im oberen Totpunkt befindet.
Auf der linken Motorseite gibt es dafür zwei kleine Deckel, die ich öffne.
Hinter dem Deckel in der Mitte befindet sich ein Sechskant, an dem ich die Kurbelwelle drehen kann.
Hinter dem kleineren Deckel am oberen Rand, sehe ich die Totpunktmarkierung. Sie zeigt mir an, wann sich der Kolben des ersten Zylinders im oberen Totpunkt befindet.
Ich drehe die Kurbelwelle, bis die Markierung mit dem „T“ wie „Totpunkt“ mit der Markierung am Gehäuse übereinstimmt.
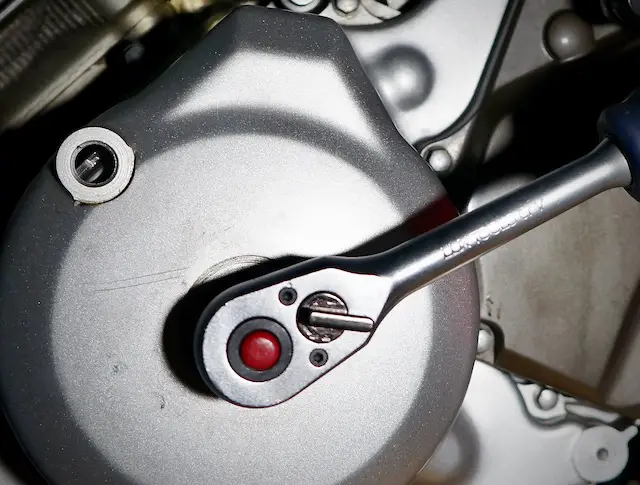
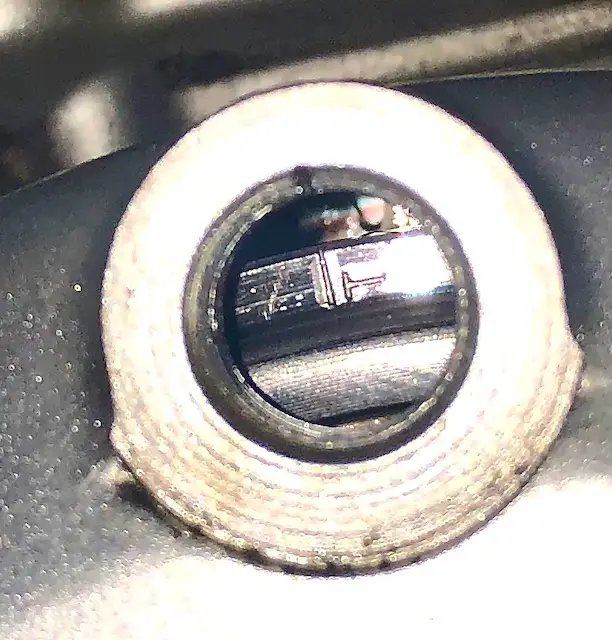
Jetzt muss ich noch überprüfen, ob sich der Zylinder im Arbeitstakt oder im Gaswechseltakt befindet.
Zur Ventilspielkontrolle brauche ich den Arbeitstakt. Im Arbeitstakt haben die Ventile Ventilspiel.
Im Totpunkt der Gaswechseltakte sind alle Nocken mit den Ventilen im Kontakt, die Auslassventile sind noch offen, die Einlassventile öffnen sich schon (Ventilüberschneidung). In dieser Position ist kein Spiel vorhanden und es kann demzufolge auch nicht gemessen werden.

Steht die Nockenwelle auf Ventilüberschneidung, muss ich die Kurbelwelle um eine volle Umdrehung weiter drehen. Dabei macht die Nockenwelle eine halbe Umdrehung und befindet sich dann in der richtigen Position.
Ich erkenne den Arbeitstakt daran, dass die Nocken der beiden Nockenwellen nach schräg oben, außen zeigen. (Im Bild siehst du die Nocken eingekreist) In diesem Totpunkt ist bei beiden Nocken Spiel zwischen Nocken und Tassenstößel.

Hinter dem Steuerkettenrad befindet sich eine kleine Markierung auf der Nockenwelle, welche beim Arbeitstotpunkt des ersten Zylinders genau oben in der Mitte steht. Diese Markierung ist eine weitere Möglichkeit um den Arbeitstotpunkt zu erkennen. Sie funktioniert allerdings nur beim ersten Zylinder.
Du siehst auch, dass die Einlassnocken des zweiten Zylinders in dieser Position die Ventile geöffnet halten. Hier kann man jetzt nichts messen.
Ventilspiel prüfen
Jetzt kann ich das Ventilspiel des ersten Zylinders prüfen.
Hier die Herstellervorgaben für das korrekte Ventilspiel der TRX:
Einlassventil | 0,15 bis 0,20 mm |
Auslassventil | 0,25 bis 0,30 mm |
Zur Ventilspielkontrolle wird eine Fühllehre mit Blättchen in 0,05 mm Stufen benutzt. Ich beginne mit dem kleineren Wert der Herstellervorgabe, also mit 0,15 mm an den Einlassventilen.
Die Lehre muss mit einem leichten Widerstand in den Spalt geschoben werden können.
Passt sie nicht in den Schlitz, dann ist das Ventilspiel zu klein.
In diesem Fall probiere ich dann die 0,10 Lehre. Je nachdem wie leicht die Lehre sich bewegen läßt, kann ich abschätzen welches Korrekturmaß ich später montiere, damit das Ventilspiel möglichst im ersten Versuch passt.
Geht die 0,15er Lehre sehr leicht, dann versuche ich die nächste, größere Lehre, also 0,20.
Ist auch 0,20 noch leichtgängig, dann ist das Ventilspiel an der oberen Toleranz. Solange die 0,25er Lehre nicht in den Spalt passt ist das Ventilspiel in Ordnung.
Kann ich allerdings die 0,25er Lehre auch noch in den Spalt stecken, dann ist das Ventilspiel zu groß. Auch hier kann ich wieder abschätzen wie leicht sich die Lehre im Spalt bewegen läßt.
Sind alle Einlassventile gemessen und die Werte auf dem unten gezeigten Blatt notiert, dann folgt die gleiche Prozedur an den Auslassventilen.
Da das Ventilspiel an den Auslassventilen größer sein soll, fange ich mit der 0,25er Lehre an.


Für die Kontrolle der Ventile des zweiten Zylinders, muss die Kurbelwelle weiter gedreht werden.
Nachdem ich den ersten Zylinder kontrolliert habe, drehe ich die Kurbelwelle um 270°, also eine dreiviertel Umdrehung entgegen dem Uhrzeigersinn. Jetzt steht der zweite Zylinder im Arbeitstakt.
Bei der TRX sind die Hubzapfen, auf denen die Pleuel montiert sind, um 90° versetzt. (Oder besser gesagt, um 270°). Bei anderen Zweizylindermotoren können es auch 180° (eine halbe Kurbelwellenumdrehung) oder 360° (eine ganze Kurbelwellenumdrehung) sein. Die 360° Variante nennt man „Paralleltwin“, weil hier beide Kolben gleichzeitig im oberen Totpunkt stehen.
Dass der Motor links herum läuft ist eine Spezialität der TRX. „Normale“ Motoren drehen rechtsrum, also im Uhrzeigersinn. Die Blickrichtung ist dabei gegenüberliegend von der Kraftabgabeseite. Die Kupplung muss sich also auf der Rückseite des Motors befinden.
Hier im Video siehst du das Messen des Ventilspieles.
Ich habe gemessen, dass die Auslassventile ein korrektes Ventilspiel haben. Die Einlassventile des zweiten Zylinders haben ein zu kleines Ventilspiel und zwei Ventile des ersten Zylinders sind an der unteren Grenze.
Das Ventilspiel muss also eingestellt werden.
Ich habe mir ein Blatt vorbereitet, auf dem ich die gemessenen Ventilspiele der einzelnen Ventile eintrage. Später, nach dem Ausbau der Nockenwelle, kann ich die Dicke der montierten Shims und die Dicke der Shims eintragen, die ich einbauen muss, damit das Ventilspiel stimmt.

In den Kreisen siehst du das gemessene Ventilspiel des jeweiligen Ventils. Die Zahl darunter ist die Dicke der installierten Original- Shim. Diese sehe ich natürlich erst, nachdem ich die Nockenwelle ausgebaut habe.
Darunter steht die korrigierte Shim- Dicke, die für das korrekte Ventilspiel sorgen soll.
Wie die Korrektur des Ventilspiels erfolgt, zeige ich in einem eigenen Blogpost.
Ventildeckel montieren
Wenn bei dir das Ventilspiel stimmt, kannst du nun den Ventildeckel wieder aufsetzen. Ich musste ja vorher noch einige Ventile korrigieren.
Die Dichtfläche des Ventildeckels und des Zylinderkopfes muss sauber sein. Wie du an den schwarzen Streifen auf den Bildern erkennen kannst, muss ich Reste der Dichtung erst noch entfernen.
Bitte aufpassen, dass keine Gummi- oder Dichtmassebröckchen in den Motor fallen.
Im Normalfall sollten sie zwar im Ölfilter gefangen werden, im Unglücksfall verstopfen sie eine Ölbohrung und verursachen Schaden. Also lieber nichts riskieren und sauber und sorgfältig arbeiten.
Ich habe mir eine neue Dichtung im Internet bestellt.
Ich dachte ich könnte etwas Geld sparen, indem ich eine Nachbaudichtung aus Italien für den halben Preis kaufe. War leider ein Irrtum, die Dichtung war zu groß und passt überhaupt nicht.
Also musste ich dann doch eine Yamaha Originaldichtung für teuer Geld kaufen.





Damit die Gummidichtung richtig dicht wird, trage ich auf den Dichtflächen ganz dünn eine, für Motoren geeignete Silikondichtmasse auf.
Besonders an den Stellen der Halbmonde traue ich dem Anpressdruck der Dichtung nicht richtig. Deshalb muss gerade an den Stellen Dichtmittel vorhanden sein.
Auf den übrigen Flächen wird das Silikon sehr sparsam aufgetragen. Ich will auf keinen Fall, dass sich innen im Zylinderkopf, wo ich nicht mehr herankomme, Dichtmittelraupen bilden.
So jetzt sieht das schon fertig aus.
Die Ventildeckelschrauben werden mit 10 Nm Anzugsmoment angezogen. Bei diesen Schrauben bin ich sehr vorsichtig. Das Mutterngewinde befindet sich im Alluminium- Zylinderkopf. Wenn das überdreht wird, dann wir es teuer und aufwändig. Also lieber Vorsicht walten lassen.
Den Rest zusammenbauen
Nun kann ich schrittweise alle anderen Teile wieder anbauen. In umgekehrter Reihenfolge, wie ich sie ausgebaut habe.
Fazit
Du siehst, die Ventilspielkontrolle ist nicht schwierig und man kann auch wenig falsch machen.
Es ist allerdings schon einiges an Arbeit.
Stimmen die Werte nicht und das Ventilspiel muss korrigiert werden, dann wird es allerdings komplizierter und hierbei können dann auch Fehler passieren, die ärgerliche Konsequenzen haben. Besonders beim DOHC Motor, bei dem die Nockenwelle ausgebaut werden muss, sollte man wissen worauf alles zu achten ist.
Aber auch das erkläre ich dir in einem nächsten Artikel.
Du darfst mir gern ein Feedback zu diesem Artikel hier lassen! Wie hat es dir gefallen? Fehlt dir etwas?
Lass es mich wissen, damit ich dazu lerne und meine Artikel immer besser werden.
Hast du toll dargestellt. Ich danke dir. Die TDM ist schon ganz schön verbaut aber zum fahren wunderbar.
Die detaillierte Anleitung zur Ventilspielprüfung ist echt hilfreich, besonders wenn man sich zum ersten Mal daran wagt. Allerdings wäre es vielleicht besser, das Ganze einem Fachmann zu überlassen, vor allem, wenn man sicherstellen will, dass der Motor optimal läuft und keinen Schaden nimmt.
Als ich meinen Oldtimer restaurieren ließ, habe ich mich für eine professionelle Bewertung entschieden, um den Wert und Zustand genau zu kennen. Ein unabhängiger Sachverständiger kann da wirklich Gold wert sein.
Klar, man sollte man sich gut überlegen, was man tun will. Oldtimer besitze, Oldtimer fahren oder Oldtimer reparieren. Meine Reparaturtipps sind für diejenigen, die Freude an letzterem haben. Aber natürlich rate ich jedem zum Fachmann zu gehen, wenn man sicher sein will, dass nichts passieren kann. Dann aber dringend darauf achten, dass es wirklich ein echter Fachmann ist! Die sind heutzutage manchmal gar nicht mehr so leicht zu finden.